
Il vapore nell’industria manifatturiera è stato quest’anno al centro del nostro progetto di ricerca e sviluppo EMS STEAM, dal nome del nostro Energy Management System e dall’acronimo STEAM (vapore in inglese): Supporta la Transizione Energetica delle Aziende Manifatturiere. Il 25 giugno ne abbiamo parlato nel corso di un webinar in collaborazione con Cannon Bono.
I generatori di vapore sono impianti ottimizzati per funzionare ad altissima efficienza, in un range molto ampio di funzionamento. Ma a tutto c’è un limite. Dal monitoraggio e analisi di numerosi generatori abbiamo ricavato i valori di efficienza (contenuto energetico del vapore prodotto diviso per il consumo di gas metano).
Il rendimento si mantiene molto elevato in un ampio intervallo di funzionamento ma sotto una certa potenza (indicativamente al di sotto del 25% della potenza nominale) si ha un brusco decadimento delle prestazioni: un vero e proprio crollo. Questo dimostra come sia essenziale dimensionare correttamente i generatori.
La prassi è: sostituisco il vecchio generatore con uno di pari potenza, o magari anche un po’ più potente (“non si sa mai”, è il solito mantra). I dati dimostrano che, invece, è importante analizzare nel dettaglio qual è il profilo di carico delle utenze e acquistare un generatore di potenza adeguata: si risparmia sia in CAPEX, che in OPEX.
Un secondo aspetto affrontato nel corso del progetto EMS Steam riguarda la gestione ottimale della pressione di vapore, sulla base del reale fabbisogno del processo produttivo. Numerosi processi produttivi hanno un funzionamento discontinuo: il fabbisogno di vapore è presente in alcune ore della giornata; in altre sono presenti solo alcune utenze, con un fabbisogno molto basso.
Sono molti i settori dove sono presenti processi produttivi discontinui, ne citiamo alcuni come esempio: agro alimentare, tessile, chimico farmaceutico. In tutti questi processi è possibile gestire il vapore in modo efficiente. Per farlo è essenziale conoscere in ogni istante il fabbisogno delle utenze. Per questo motivo nel corso del progetto EMS Steam abbiamo esteso il nostro digital twin al di fuori dei confini della centrale termica, includendo le utenze.
Costruito il digital twin, lo abbiamo applicato ad un caso concreto, un caseificio di Parmigiano Reggiano nella provincia di Parma.
Il caseificio è caratterizzato da:
- Produzione molto variabile: un picco di produzione di 3-4 ore (60% del consumo); mantenimento per il resto della giornata (40% del consumo)
- Tempo a carico parziale (<20%): 75-85%
- Nei periodi di non produzione (mantenimento) presenti alcune utenze minori: CIP, climatizzazione magazzino etc…
Grazie a questa variabilità è possibile gestire il vapore a pressione variabile con importanti risultati in termini di risparmio.
Nel periodo di mantenimento si registra una diminuzione del consumo di gas tra il 12% e il 20%.
L’effetto è molto alto perché la caldaia lavora a bassa efficienza in quelle ore e quindi la riduzione della pressione incide in modo significativo sui consumi.
è inoltre importante verificare che il servizio reso dalla centrale non sia in nessun modo compromesso dall’ottimizzazione implementata. Numerosi test hanno consentito di verificare l’assenza di effetti sul servizio.
Qui sotto un grafico con i risparmi.
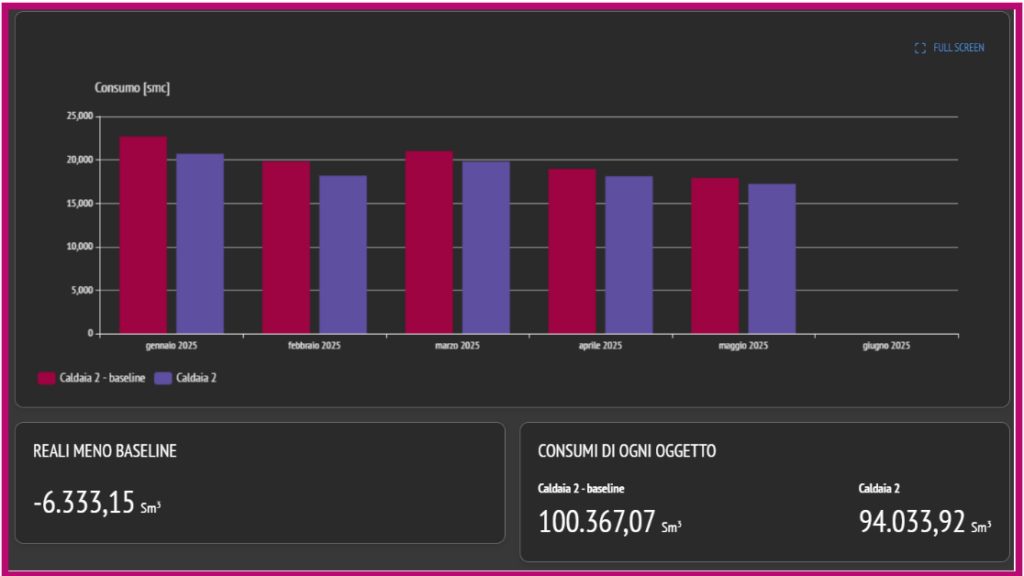
Infine, abbiamo verificato dall’analisi dati che è possibile integrare una pompa di calore per coprire le utenze nella fase di mantenimento. L’installazione di una pompa di calore consentirebbe una riduzione complessiva del 40% nel consumo di gas naturale, con una riduzione dei costi operativi superiori al 10%.
Iniziativa realizzata con il contributo del Programma FESR, Fondo Europeo di Sviluppo Regionale di Regione Lombardia. Il Progetto è realizzato con il concorso di risorse dell’Unione europea, dello Stato italiano e di Regione Lombardia, in applicazione del Regolamento (UE) 2021/1060 articoli 46,47, 50 e allegato IX.
